Downloads
Download


This work is licensed under a Creative Commons Attribution 4.0 International License.
Article
Experimental Study on the Deflagration to Detonation Transition of Hydrogen Mixture under Elevated Pressure and Temperature Conditions
Xiao Yu, Long Jin, Linyan Wang, Navjot Sandhu, and Ming Zheng *
Department of Mechanical, Automotive and Materials Engineering, University of Windsor, 401 Sunset Avenue, Windsor, ON N9B 3P4, Canada
* Correspondence: mzheng@uwindsor.ca
Received: 26 March 2025; Revised: 7 April 2025; Accepted: 14 April 2025; Published: 24 April 2025
Abstract: In this paper, the deflagration to detonation transition (DDT) process of a hydrogen-air mixture is investigated using a small tube with an inner diameter of 11.1 mm. A rapid compression machine (RCM) is utilized to compress the mixture, attaining high pressure and temperature to resemble engine applications. Both piezoelectric pressure transducers and ion sensors are used to detect the flame front, calculating the flame propagation speed. The background absolute pressure before DDT is adjusted from 20 kPa to 810 kPa via a combination of charging pressure and RCM compression, while the background temperature is adjusted from 296 K to 460 K with spark timing adjustment after the compression process of RCM. It is observed that background pressure is an important parameter that decides the existence of a successful DDT process, while background temperature offers a limited contribution to accelerating the flame speed within 1 m tube length.
Keywords:
deflagration to detonation transition rapid compression machine elevated background pressure flame acceleration1. Introduction
Decarbonization has been the major trend for research and development activities in the transportation sector in recent years to reduce the environmental impact of automotive vehicles, maritime, and airplanes. Presently, low-carbon and zero-carbon fuels are of specific interest, such as renewable natural gas [1], hydrogen [2–4], and ammonia [5]. However, for low-reactivity fuels, such as natural gas and ammonia, further improvement in combustion efficiency is needed to reduce the direct emission of methane and ammonia, as well as enhance the system efficiency [6–8].
For spark ignition engines, an efficient combustion event relies on a rapid flame propagation process, which is challenging for fuels with lower laminar flame speeds. To tackle this challenge, a stronger in-cylinder turbulence is needed to shorten the combustion duration, accompanied by strong ignition sources to secure the flame kernel initiation.
For internal combustion engines, the in-cylinder turbulence is usually initiated by the piston movement [9] and can be intensified by proper design of the intake manifold and combustion chamber geometry [10]. Under these conditions, advanced ignition techniques are developed for stable combustion process using lean or diluted mixtures, such as enhanced discharge current [11], prolonged discharge duration [12], enhanced ignition volume [13–16], low temperature plasma sources [16–19], and prechamber ignition systems [20].
Prechamber ignition systems reduce the combustion duration significantly to increase thermal and combustion efficiencies. The high-speed flame/radical jet shooting out from the orifices of a prechamber spark plug can increase local turbulence intensity near the spark plug, as well as enlarge the ignition area [21]. Furthermore, an active prechamber ignition system injects fuel directly into the prechamber to modulate the local fuel-air ratio, which partially solves the scavenging challenge a passive prechamber normally has and can organize stable combustion process of ultra lean mixtures [22]. Such ignition systems also provide the possibility to use fuels with higher flame speed, such as hydrogen, to ignite the low chemical reactivity fuel in the main combustion chamber. It has been reported that the flame/radical jet speed can reach supersonic under certain conditions [23–26].
When flame speed is further increased to a couple of thousand meters per second, the flame transforms into a detonation wave, which has demonstrated its ability to further improve the efficiencies of gas turbines used in supersonic aircraft and electricity generation [27]. The detonation waves propagate around the Chapman-Jouguet (CJ) velocity [28] to generate a constant-volume combustion process of the fuel-air mixture, known as the Humphrey cycle [29]. For pulsed detonation engines, the fresh air-fuel mixture is introduced in the combustion chamber in the periodic cycle from 10 to 100 Hz [30]. The detonation speed of a fuel-air mixture is less sensitive to the chemical property of the fuel compared with the laminar flame speed, as demonstrated in Figure 1, which provides the possibility to utilize fuel with a lower laminar flame propagation speed for high-speed combustion applications under detonation mode [31–44].
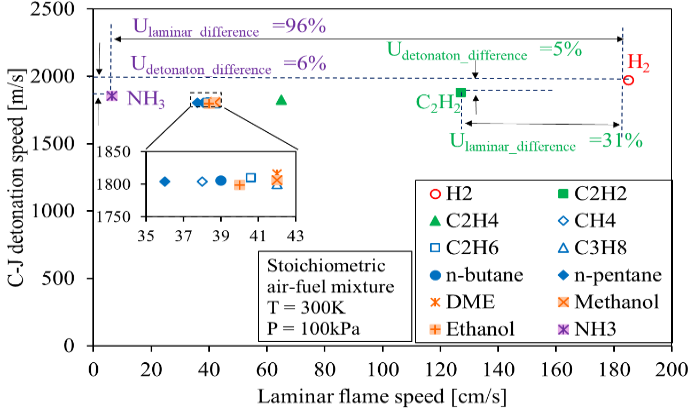
Figure 1. Calculated C-J detonations speed under ambient pressure and temperature, and laminar flame speed of various fuels.
For real applications, the transition process from deflagration to detonation flame needs to be considered because the direct initiation of a detonation flame demands a significant amount of energy [26]. A deflagration flame accelerates when it passes through a tube and may eventually reach detonation velocity [45], known as the deflagration to detonation transition (DDT) [46]. Presently, most of the DDT process and steady-state detonation investigations are aiming to avoid the explosion of fuel or combustible mixtures, including the nuclear reactor [47], hydrogen storage [48], liquid hydrogen handling [49], and detonation-based propulsion systems [50–54]. Therefore, the majority of the DDT research found in literature is under vacuum to atmospheric conditions at room temperature, with some exceptions for specific research purposes [55]. Manzhalei et al. experimentally conducted a quantitative analysis of the cell size measurement of H2/O2 detonation under initial pressure up to 10 atm with a metallic tube [48]. The results suggest that the detonation front remains mostly constant even when subjected to high initial pressure based on observations of phenomena. In 2007, Ng et al. utilized the Zel’dovich-von Neumann-Dӧring (ZND) model coupled with detailed chemical kinetics to gain an understanding of the detonation within a similar pressure range. Tieszen et al. investigated the impact of initial temperature on the detonation process with a heated detonation tube. The detonation cell size is measured with initial temperature from 298 K to 373 K under atmospheric pressure [56].
In this paper, the DDT process of hydrogen air mixture is experimentally investigated under pressurized conditions to discuss the potential of using hydrogen detonation as the ignition source for high energy density applications. The inner diameter of the tube is 11.1 mm, which is smaller than most of the detonation research reported. As summarized in Table 1, in previous research, the detonation tube or channel has an inner diameter range from 77~430 mm when studying detonation with hydrogen air mixture, and 12~200 mm for hydrogen/oxygen mixture. Reactive fuels with smaller detonation cell sizes, such as C2H2 and H2, typically allow a smaller inner diameter to investigate DDT, including using tube diameter as small as 1 mm with pure hydrogen/oxygen mixture [37]. For more practical fuels with relatively low chemical reactivity, such as air-fuel mixture using methane or propane fuel, the tube diameter is relatively large, from 30 mm [38] to 520 mm [39], to realize the DDT transition process [40]. However, the combination of a small-diameter tube with high initial pressure and temperatures is scarcely reported.
Mixtures | Dilution [%] | P initial [kPa] | T initial [K] | Ø | ID [mm] | Authors | Ref. |
---|---|---|---|---|---|---|---|
H2/O2 | - | 20–800 | 293 | 1 | Ø105 | Kuznetsov et al. | [46] |
- | 20.3–1230 | 293 | 1 | Ø12 | Manzhalei | [48] | |
- | 0.4-1 | 77 | 0.4 | Ø52 | Shen | [49] | |
- | 101.3 | 293 | 0.4–1.9 | Ø120, Ø300 | Litchfield et al. | [57] | |
- | 70.11 | 293 | 1 | Ø200 | Zitoun | [58] | |
- | 49.1–98.3 | 123 | 1 | Ø200 | Zitoun | [58] | |
- | 101.3 | 293 | 0.3–2 | Ø6.5–Ø53 | Matsui | [59] | |
- | 28.4–99 | 293 | 1 | Ø52 | Desbordes | [60] | |
- | 5.2–20.1 | 293 | 1 | Ø50.8 | Knystautas | [61] | |
- | 5.4–33.1 | 293 | 1 | Ø50.8 | Strehlow | [62,63] | |
- | 50 | 298 | 1 | 50x50 | Liberman et al. | [64] | |
- | 18.8–45.9 | 293 | 1 | Ø50 | Lee | [65] | |
- | 13.6–89.8 | 293 | 1 | Ø27 | Voytsekhovskiy | [66] | |
- | 8–40 | 293 | 0.06–4.5 | 20 × 20 | Wang et al. | [67] | |
- | 100 | 293 | 0.2–11.3 | Ø4–Ø20 | Bykov et al. | [68] | |
- | 4.5–118.0 | 293 | 1 | Ø16 | Denisov | [69] | |
- | 7.1–52.4 | 298 | 1 | - | Barthel | [70] | |
- | 100 | 135 | 0.1–3.6 | - | Agafonov | [71] | |
- | 100 | 298 | 0.1–4.3 | - | Agafonov | [71] | |
- | 150–300 | 373 | 0.4–3.0 | Ø430 | Tieszen | [35] | |
H2/Air | - | 101.3 | 293 | 0.4–5.6 | Ø430 | Guirao | [45] |
- | 100 | 278–370 | 0.51 | Ø430 | Tieszen | [52] | |
- | 100 | 288–373 | 0.51 | Ø430 | Tieszen | [52] | |
- | 101.3 | 298 | 0.4–5.5 | Ø430 | Tieszen | [52] | |
- | 100 | 298 | 0.4–3.7 | - | Agafonov | [71] | |
- | 82.7 | 293 | 0.5–0.8 | 1830 × 2440 | Benedick | [72] | |
- | 100–240 | 650 | 0.2–0.4 | Ø100 | Ciccarelli | [73] | |
- | 100 | 500 | 0.3–1 | Ø100 | Ciccarelli | [73] | |
- | 100 | 300 | 0.4–2.5 | Ø100 | Ciccarelli | [73] | |
- | 100 | 393 | 0.4–3.0 | Ø430 | Stamps | [74] | |
- | 23.9–252.2 | 293 | 0.5 | Ø430 | Stamps | [75] | |
- | 25.5–151.3 | 293 | 1 | Ø430 | Stamps | [75] | |
- | 10–101.5 | 293 | 1 | Ø152 | Kaneshige | [76] | |
- | 101.3 | 293 | 0.5–3.6 | Ø150 | Guirao | [77] | |
- | 100 | 293 | 2.38 | Ø141 | Wang et al. | [78] | |
- | 101 | 293 | 0.3–2.1 | Ø100 | Cross et al. | [79] | |
- | 83–961 | 293 | 1 | Ø77 | Bull et al. | [80] | |
- | 101.3 | 294 | 0.6–1.4 | Ø77 | Atkinson | [80,81] | |
- | 100 | 293 | 1–1.7 | 34 × 2.2 | Dorofeev et al. | [82] | |
- | 101.3 | 293 | 0.6–3.9 | - | Makeev | [83] | |
40 | 12–33 | 293 | 0.36 | Ø50.8 | Strehlow et al. | [62] | |
H2/Air/Ar | 40 | 13–26 | 293 | 2.12 | Ø50.8 | Strehlow et al. | [62] |
- | 18.8–45.9 | 293 | 1 | Ø50 | Lee | [65] | |
0–85 | 6.1–52.8 | 298 | 1 | - | Barthel | [70] | |
81–91 | 100 | 298 | 1 | - | Agafonov | [71] | |
25–84 | 106.6 | 293 | 1 | Ø150 | Kumar | [84] | |
50 | 27.2–83.2 | 293 | 1 | 51 × 51 | Anderson | [85] | |
70 | 14.6–46.9 | 293 | 1 | Ø50.8 | Srehlow | [62,63] | |
H2/Air/He | 70–88 | 100 | 298 | 1 | - | Agafonov | [71] |
25–87 | 106.6 | 295 | 1 | Ø150 | Kumar | [84] | |
40–87 | 106.6 | 333 | 1 | Ø150 | Kumar | [84] | |
62–87 | 106.6 | 373 | 1 | Ø150 | Kumar | [84] | |
10–80 | 27.5–161 | 295 | 1 | Ø150 | Kumar | [84] | |
31–56 | 101.3 | 293 | 1 | Ø50.8 | Knystautas | [61] | |
H2/O2/N2 | 55–78 | 100 | 298 | 1 | - | Agafonov | [71] |
25–50 | 100 | 293 | 1 | Ø152 | Kaneshige | [76] | |
21–79 | 100 | 293 | 1 | Ø200 | Liu et al. | [86] |
In this study, a rapid compression machine is connected to a tube with an inner diameter of 11.1 mm to investigate the deflagration-to-detonation process of premixed hydrogen air mixtures with oxygen enrichment. A rapid compression machine is connected to the outlet end of the detonation tube to increase the initial pressure and temperature simultaneously. It was found that the H2/air case receives challenge to accelerate when traveling through the tube under such small tube diameter under room temperature. Reducing the nitrogen dilution ratio and increasing the initial background pressure is utilized to investigate the deflagration to detonation process under the temperature of 460 K.
2. Experimental Setup
2.1. Detonation Tube Setup
An in-house designed ion-current module was used to detect the ionization process during the flame propagation from the inline resistor, and the detailed electrical circuit is shown in Figure 2. The bias voltage is regulated to 50 V from the boosted 9 V battery, and the circuit is isolated to acquire smooth signals. The inline resistance is 1 MΩ for increasing the measurement resolution since the ion current is usually in the microampere (μA) level. Hence, the ion current can be calculated as shown in Equation (1).
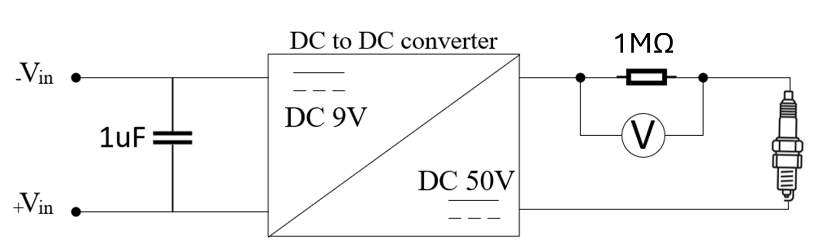
Figure 2. Ion current sensing circuit.
Both ion-current and pressure measurements are collected to determine the arrival timing of the flame front in order to calculate the average flame propagation speed between the measurement points. In this paper, the timing of the flame front arrival is characterized by the rise of the ion current signals because it is more sensitive under various flame propagation speeds. A more detailed description is provided in Section 3.2. A typical pressure and ion current measurement of a deflagration flame is demonstrated in Figure 3. Under the low energy density of air-fuel mixtures, the combustion pressure is generally low, and the amplitude can be incorrectly indicating the flame arrival time due to the shock precursor. The concern can be addressed by employing the ion-current sensor, as the ionization remains unaffected by the acoustic wave. Therefore, the flame speed is mostly calculated from the ion-current sensor with respect to the distances between the measurement points, as shown in Equation (2). The total combustion duration is defined as the time between spark timing and the peak pressure timing at measurement position 4. The shorter duration promotes faster flame propagation, and the high turbulence flow may compensate for the heat loss to the wall for achieving the DDT process.

Figure 3. Ion current and pressure measurement of deflagration flame of hydrogen/air mixture.
Figure 4 shows the schematic of the detonation tube. The diameter of the detonation tube is 11.1 mm, with a total length of 1 m. The length/diameter ratio of the tube, L/d, is 90. A chamber is connected to one end of the detonation tube, with an inner diameter of 15.5 mm and a length of 20 mm. The chamber is equipped with gas exchange ports and a sparkplug for ignition. Four measurement points are placed along the flame propagation direction, each with a piezoelectric pressure transducer (PCB 113B22) and a miniature sparkplug (RIMFIRE VR2L), arranged opposed to each other, as shown in Figure 4. The miniature sparkplugs were used as ion sensors to detect the arrival of the flame front.
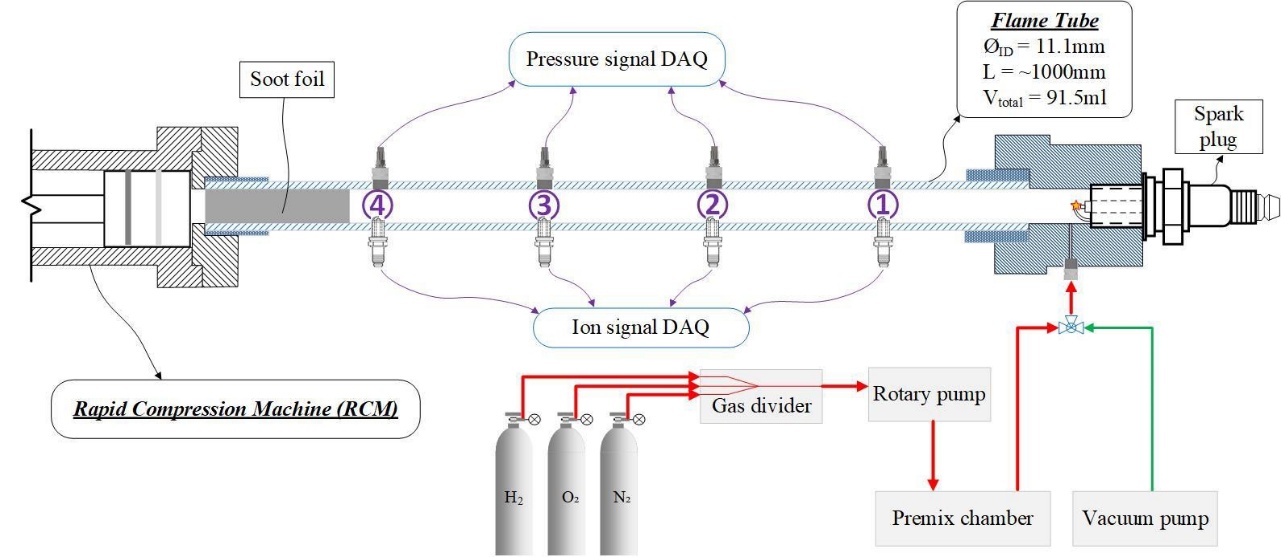
Figure 4. Schematic diagram of the detonation tube section in the setup.
2.2. Rapid Compression Machine
A rapid compression machine is utilized to increase the initial pressure and temperature before the ignition event. The present RCM system is designed with pneumatic driving and hydraulic braking to compress the air-fuel mixture within 15~20 ms with a compression stroke of 223 mm, as shown in Figure 5. A reed switch is installed to detect the initial movement of the pneumatic piston at the beginning of the compression stroke, and the piston movement signal is used as a trigger to synchronize the timing of ignition and data acquisition. A detailed description of the RCM setup can be found in the author’s previous publications [12,87,88]. The inner diameter of the compression cylinder is 50 mm. Considering the volume of the detonation tube (~91.5 mL), the geometric compression ratio of the RCM is 4.6:1 after it is connected with the detonation tube.
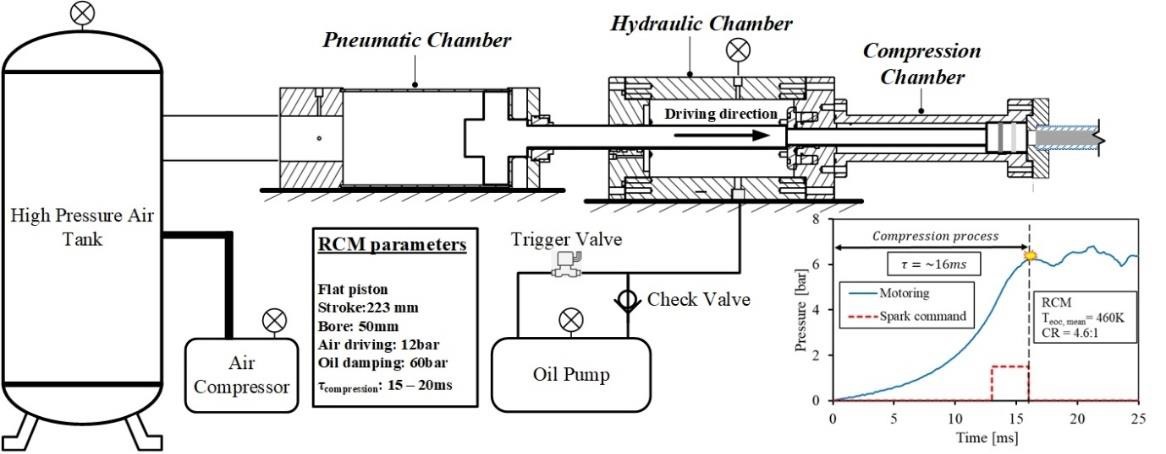
Figure 5. Schematic diagram of the RCM section in the setup.
A premixing chamber is employed to supply a premixed mixture to the detonation tube. The test platform operates in hybrid mode, which utilizes a combination of compressed and non-compressed conditions to cover the absolute pressure ranges from 20 kPa to 1600 kPa. When the initial pressure is below atmosphere, the pressure from the pre-mixing chamber is employed. The compression piston was fixed at the end-of-compression position and held by the pressurized pneumatic cylinder at 1.2 MPa pressure, which can secure the position of the compression piston up to 10.8 MPa in the compression cylinder. For initial pressure greater than the storage pressure of the premixing chamber, a compression process is needed to further increase the initial pressure.
During the compression process, the mixture undergoes an adiabatic compression process, which increases both the in-cylinder pressure and temperature. Therefore, it is necessary to postpone the ignition timing for a specific duration after the compression process in order to fix the initial temperature. For one second after the start of the compression process, the mixture temperature is close to the ambient temperature.
A set of tests is performed to measure the in-cylinder temperature profile after the compression process, and it is decided to fix the spark timing delay at one second after the compression process to reach an ambient temperature. A shorter spark timing delay would have a higher initial temperature, which affects the DDT process, while a longer spark timing delay would cause heat loss to the wall. The test result of the one-second delay is demonstrated in Figure 6 to show the impact of the compression process on the flame speed of oxygen-enriched methane air mixture under similar initial temperatures. It is observed that both the flame acceleration trend and flame speed under similar initial pressure agree with each other, validating the present testing scenario.
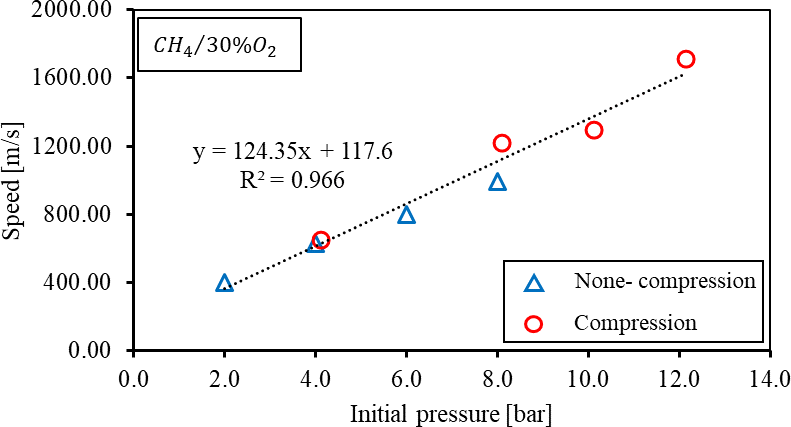
Figure 6. Comparison of flame propagation speed of compression and non-compression cases under the same initial temperature.
2.3. Mixture Preparation and Methodology
An Environics 4040 series gas divider, manufactured by Environics that located in Tolland, CT, United States, is utilized to mix hydrogen with air and oxygen. The device incorporated four mass flow controllers prepared with premixed mixtures of up to four different species with an accuracy of parts per million (ppm). The output pressure of the gas divider is set to 200 kPa, then compressed to 900 kPa by a chemical diaphragm pump and stored in a premixing chamber. The pressurized mixtures are stored for at least an hour-long period to reach stable thermodynamic conditions.
A vacuum pump is utilized to evacuate the compression chamber and the detonation tube for each test before introducing the fresh air-fuel mixture. The vacuum process is performed twice to ensure the consistency of the initial mixture composition. This is especially important for test cases under low initial pressures. The specific concentrations of these mixtures, measured in terms of volume, are provided in Table 2.
Excess Air-Fuel Ratio (λ) |
Testing Condition (With RCM) | Fuel Compositions Volume % | Initial Absolute Pressure (before Ignition), kPa | Initial Temperature (before Ignition), K | ||
---|---|---|---|---|---|---|
H 2 | O 2 | N 2 | ||||
1 | Non-Compression | 29.58 | 14.79 | 55.63 |
50, 80, 100, 110, 120, 150, 200, 300, 650 |
296 |
41.18 | 20.58 | 38.24 | 40, 50, 80, 100, 200, 300 | |||
66.67 | 33.33 | 0 | 20, 40, 80, 100, 162, 405 | |||
Compression | 29.58 | 14.79 | 55.63 | 650 | 296, 299, 302, 323, 361, 374, 404 | |
320, 400, 490, 650, 730, 810 | 460 | |||||
66.67 | 33.33 | 0 | 80, 240, 410 |
3. Results and Discussions
3.1. Impact of Background Density on Detonation Cell Size
The detonation cell size of a mixture is commonly used to describe the length scale of a detonation structure [25,89] and predict the chemical kinetic properties [90]. Research has reported that the detonation cell size is proportional to the induction length [91], which can be affected by the background density. Cicearelli et al. examine the influence of initial pressure on detonation cell size using a detonation tube with 100 mm, and the experimental findings demonstrate consistency with the ZND model when the pressure is below 200 kPa. The authors propose that to expand upon the findings, a more sophisticated high-pressure driving system is necessary [73].
In the present setup, the detonation cell sizes of stoichiometric H2/O2 mixture under various initial pressures are first benchmarked to verify the detonation event on the present system, as presented in Figure 7 and plotted in Figure 8. The detonation cell is collected using soot foil placed close to the end of the detonation tube connected to the RCM, where a steady-state detonation event is more likely to be observed. The cell size measurements are obtained by covering the range of absolute pressure from 30 kPa to 400 kPa. As shown in Figure 8, despite the relatively smaller tube inner diameter compared with previous research, the cell size agrees well with the previous results [46,48,52,58,60–62,66,69,70,73,74], as well as the one-dimensional ZND simulation [91].
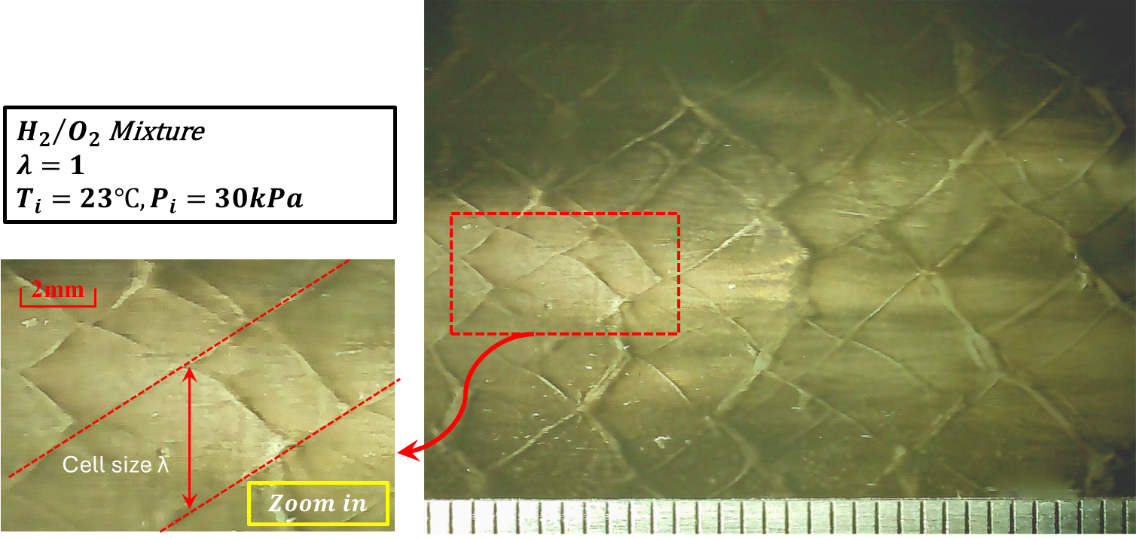
Figure 7. Detonation cell size of stoichiometric H2/O2 mixtures under initial pressure of 30 abs. measured in the Φ11.1 mm tube using stainless steel soot foil.
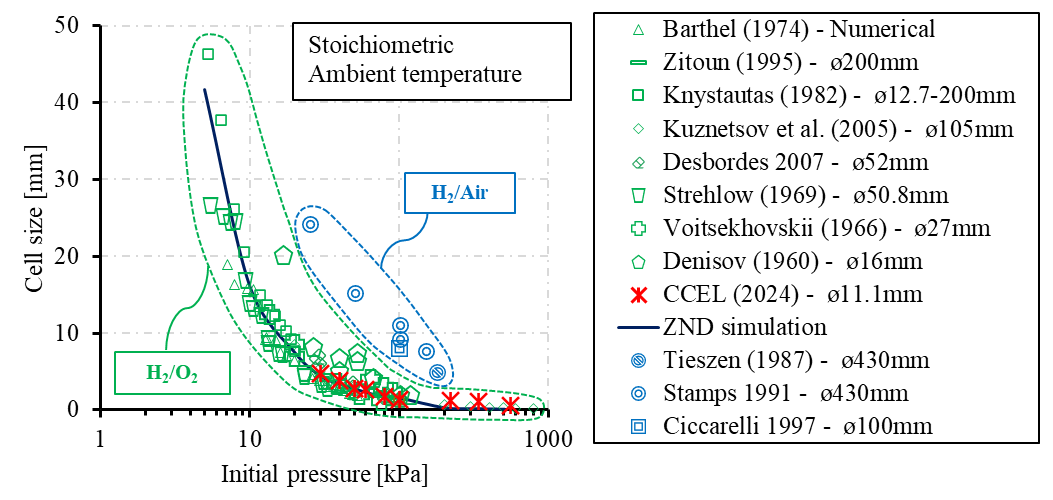
Figure 8. Cell size measurement on H2 detonation research [46,48,52,58,60–62,66,69,70,73,74].
3.2. Detection of Deflagration and Detonation Flame Front
Presently, for steady state detonation research, the arrival of the detonation front can be measured via optical, ion, and pressure signals. In this study, both ion current and pressure signals are used to detect the arrival of the flame front for flame propagation speed calculation. The two measurement methods are used simultaneously because of the challenge of using a single detection method to precisely measure the DDT process. Figure 9 demonstrates the flame propagation process along the detonation tube under two different background pressures, and the number in each circle in the subfigures refers to the measurement position illustrated in Figure 4.
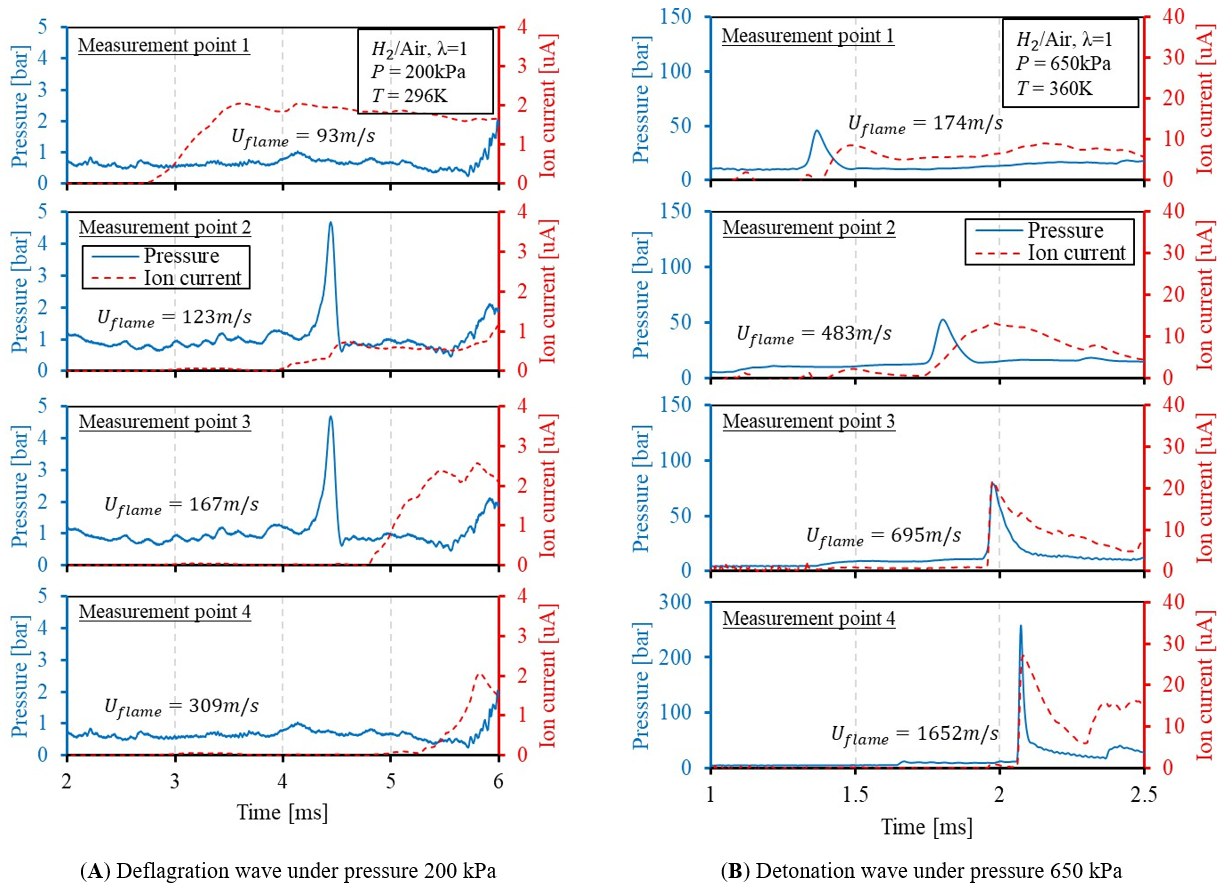
Figure 9. Pressure and ion current measurement of stoichiometric hydrogen/air mixture.
For the initial pressure of 200 kPa case, the flame speed accelerates from 93 m/s at the first measurement point to 309 m/s when it passes through the fourth measurement point, as shown in Figure 9A. However, the flame failed to reach a supersonic state while traveling through the tube under an initial pressure of 200 kPa.
For flame deflagration waves with a speed slower than the speed of sound, the flame front is an expansion wave that causes minimal local pressure to rise when passing the pressure sensors. The pressure sensors located downstream of the flame front will also measure the pressure rise caused by the heat release from the fuel even before the arrival of the flame front. Moreover, the leading shockwaves generated during the flame propagation process can also be picked up by the pressure transducers at the measurement points, making it difficult to isolate the pressure wave front and the flame front from each other. Ion current, on the other hand, is only sensitive to the ionization process, which mainly exists within the combustion zone, and it is much easier to indicate the arrival timing of the flame front, as shown in Figure 9A.
When the initial pressure is increased to 650 kPa, the flame speed gradually increases compared with the 200 kPa case but increases to 483 m/s at the second measurement point that is located 170 mm downstream from the first measurement point. The flame speed reaches 1652 m/s at the fourth measurement point, only slightly lower than the C-J velocity of the hydrogen/air mixture, which is around 2007 m/s. The supersonic deflagration waves and detonation waves can generate a high-pressure gradient at the flame front, making themselves visible on the pressure traces, as demonstrated in Figure 9B.
It is observed from point 2 and point 3 that the rising edge of the ion-current signal is synchronized with the peak of the pressure signal, indicating the arrival of the flame front. When flame speed further increases to close to the detonation stage, for example, measurement point 4 in Figure 9B with a flame speed of 1652 m/s, the timing difference between the ion current and pressure signals are negligible, indicating both are suitable to determine the detonation speed of the flame front. The ion current is quite strong because of the thermal ion generated by the high-temperature, high-pressure detonation front. In the later sections, the timing of the ion current signals is used as the primary signal to demonstrate the flame development process, as well as the flame speed calculation.
Overall, the performance of the pressure transducer and ion sensor are distinct from each other when the flame is propagating slowly but agree with each other very well when the flame speed is high. The ion-current sensing technique can detect the arrival of the combustion wave dutifully, regardless of the flame speed, because it is measuring the ions within the flame front. However, physical damage of the ion sensors or sparkplugs used as an ion probe are observed under elevated initial pressures. For a strong detonation wave traveling under high initial conditions, the peak pressure at the flame front can reach 35 to 40 MPa, as demonstrated in Figure 10. Such strong pressure waves have a higher chance of breaking the ceramic insulator of the spark plugs. This brings a safety concern of test, especially at the presence of optical windows.
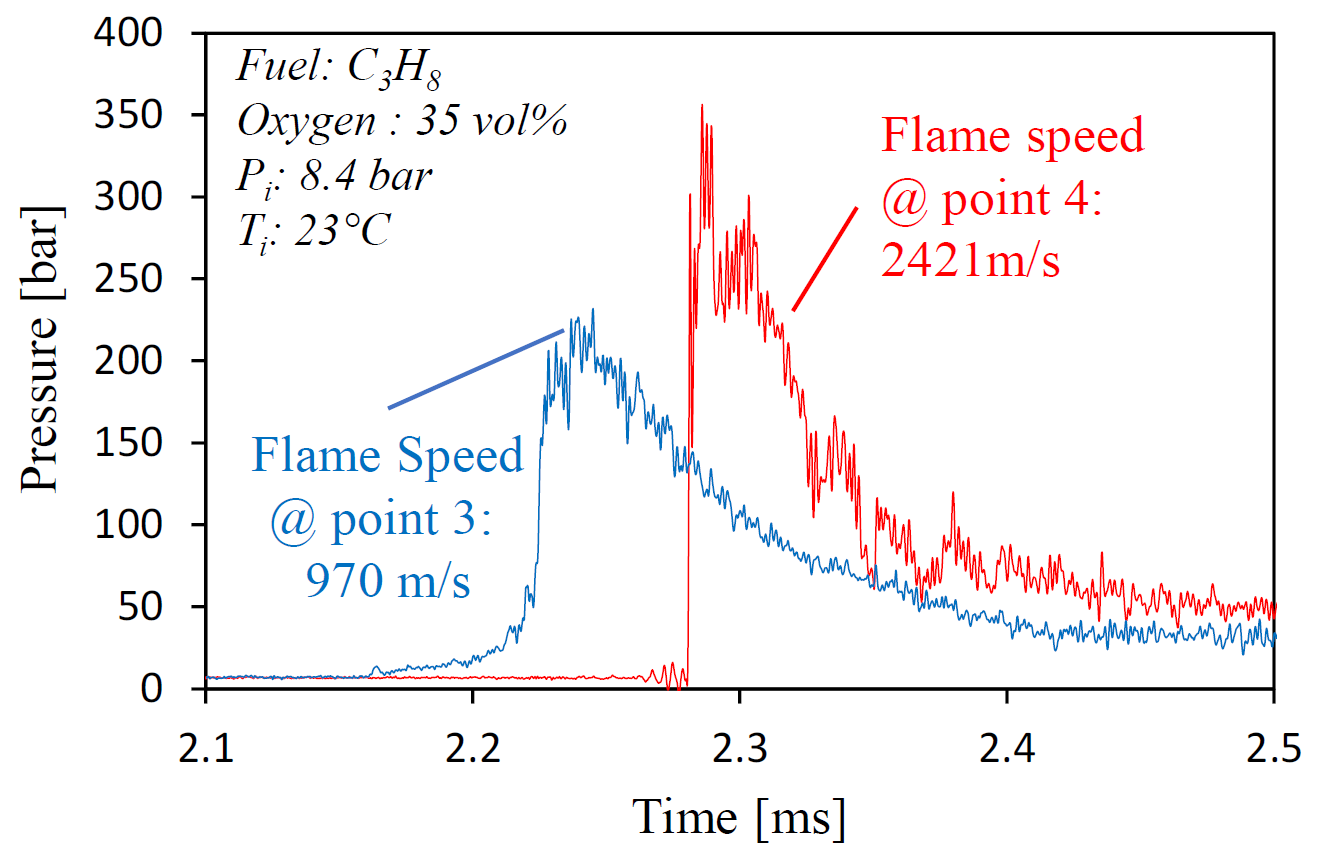
Figure 10. Peak detonation pressure reaches 35 MPa.
3.3. Deflagration to Detonation Transition of Hydrogen Mixture under Elevated Pressures
The impact of background pressure on the flame development of hydrogen fuel is investigated in this section. Three types of mixtures are used, including hydrogen/air, hydrogen/air with oxygen enrichment, and pure hydrogen/oxygen. The ion current profile on the flame propagation of H2 fuel with O2 enrichment is demonstrated in Figure 11, and the flame speed calculation is shown in Figure 12. In Figure 11A, the ionization process of H2/air continues for an extended period after the flame front reaches the measurement locations, indicating that flame propagation travels progressively and the reaction zone is extensive, as the ionization species remains detectable in the vicinity of the sensor gap. The fluctuating ion current amplitude can be observed in all the locations, and it becomes unpredictable. The behavior suggests that the flame front is unstable when travelling through the tube and localized chemical reaction can be struggled to sustain or even accelerate the flame propagation properly. On the other hand, with oxygen enrichment, in Figure 11B,C, the ionization process distinctly reveals the approach of the flame front as the steep ion current slope. The relatively stable profile of ion current with decreasing amplitude indicates the fast flame front travels through the sensor and converts reactants to the products, leading to the detonation transition.

Figure 11. Effect of pressure on flame development of Hydrogen fuel with ion current profile.
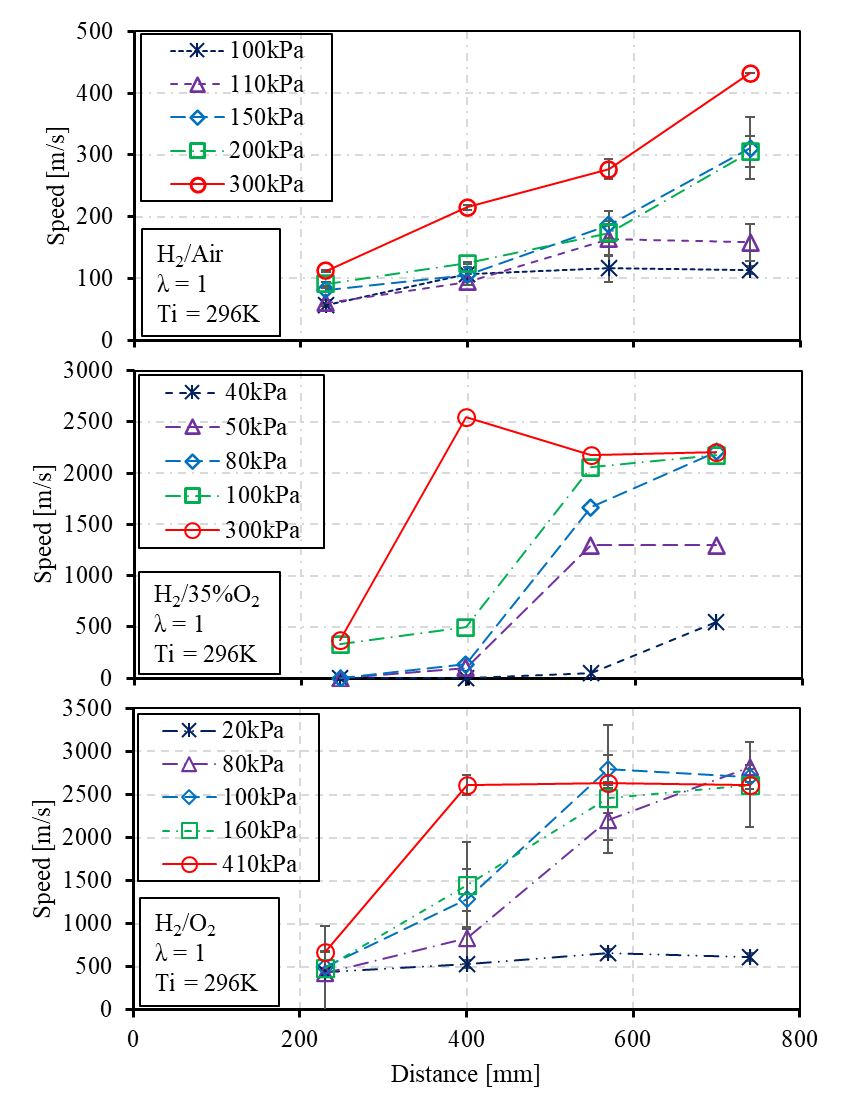
Figure 12. Impact of background pressure on the DDT process utilizing hydrogen fuel with oxygen enrichment.
The flame speed profile can be further analyzed with measurement points, as shown in Figure 12. With a 79% N2 dilution, the flame propagation can be sustained through the small diameter tube, and the acceleration is apparent to steadily develop. Despite the speed of these conditions at the final measurement point does not approach the half C-J speed, the potential tendency suggests that the transition can be obtained by further increasing initial pressure or tube length. When the dilution ratio is reduced to 75%, the range of conditions is conducted from the initial pressure of 40 to 300 kPa absolute to observe the DDT process. The vacuum condition of 50 kPa indicates that the flame tends to accelerate initially when traveling from measurement point 2 to 3 but afterwards, begins to slow down as it continues to propagate. On the other hand, the initial pressure of 80 kPa enhances the flame acceleration process from the first measurement point, resulting in a gradual increase in speed across the measurement points to present the DDT process. When the dilution is absent, the H2/O2 mixture is highly sensitive to obtain detonation [77]. The vacuum to atmosphere pressure is abundantly investigated, as seen from Table 1. This study utilizes the much smaller diameter of the 11.1mm tube to validate detonation initiation from vacuum to above-atmospheric pressure. When the initial pressure is significantly low, as a 20 kPa, the flame propagation initiates at the first measurement of 390 m/s. However, the evolution of flame speed fails to demonstrate an intention to increase, and the flame speed exhibits a reduction from measuring point 3. When the initial pressure reaches 80 kPa, the DDT process becomes apparent. The steady state detonation process can be achieved by further increasing initial pressure to 100 and 400 kPa.
Pressure and oxygen enrichment impact on the achieving detonation (CJ velocity) and the requisite duration to approach the end of tube is demonstrated in Figure 13. In the H2/air mixture case, the increased initial pressure from 100 to 300 kPa has shown gradual improvement on the flame speed at measurement point 4, but it is still challenged to approach the half C-J velocity. This can be seen from the fluctuating ion current profile and unstable ionization process in the vicinity of the sensor gap in Figure 11A. The increasing tendency suggests that higher initial pressure is required to achieve the DDT process under the present detonation tube length when the mixture is highly diluted. When the N2 dilution ratio is further reduced to 75%, the increased mole fraction of H2 improves the flame acceleration with increased reactivity of the mixture. The initial pressure of 80 kPa can significantly improve the speed at measurement point 4 to reach a steady detonation at C-J velocity. Hence, higher energy density offers fast flame acceleration with increased reactivity of the mixture. It indicates that the H2 mole fraction increased from 30% to 33%, which contributes to the significance in flame acceleration at measurement point 4. For pure H2/O2 cases, the flame speed can reach the theoretical CJ detonation velocity with initial pressure below the ambient, which is relatively close to the H2/35% O2 case. The results suggest that the enhancement of oxygen enrichment on the final flame speed becomes minimally beyond 35% O2 addition.
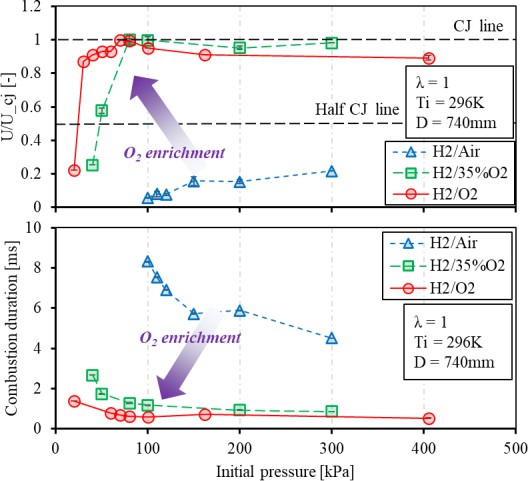
Figure 13. Pressure and oxygen enrichment impact on the achieving detonation (CJ velocity) and the requisite duration to approach the end of the tube.
Considering the combustion duration, O2 enrichment is significant to enhance the chemical reaction for the flame acceleration mechanism within the smooth tube [28]. Especially, the duration is reduced to less than 1 ms under the H2/O2 case. The improvement is shown with the increased initial pressure, and it is essential to the jet ignition source for ICEs. When the mixture is diluted to the H2/air case, the duration is prolonged to ~4 ms. The longer flame travelling potentially includes more heat loss and momentum energy to the wall. At least, it indicates that flame speed requires exceeding half CJ to acquire the shortened combustion duration
3.4. Deflagration to Detonation Transition of Stoichiometric Hydrogen Mixture under High Temperature
The initial temperature of 460 K is attributed to the adiabatic compression process of the RCM, which is being used to study the impact of initial pressure on the DDT process, as shown in Figure 14. Quantitative tests are conducted in the H2/air case since the mixture is less sensitive due to the higher N2 dilution compared to other cases. When the initial pressure increased to 400 kPa, the flame speed was capable of attaining half the C-J velocity. When the initial pressure exceeds 700 kPa, the speed at measurement point 4 becomes unaffected. Despite the considerable dilution of the mixture, the flame speed observed in the final measurements indicates that the detonation initiation can be improved by increasing the initial pressure in high-temperature conditions. In the absence of dilution, the pure H2/O2 mixtures are highly sensitive to detonation, and the initial pressure of 240 kPa indicates that the flame speed is approaching the near CJ velocity.
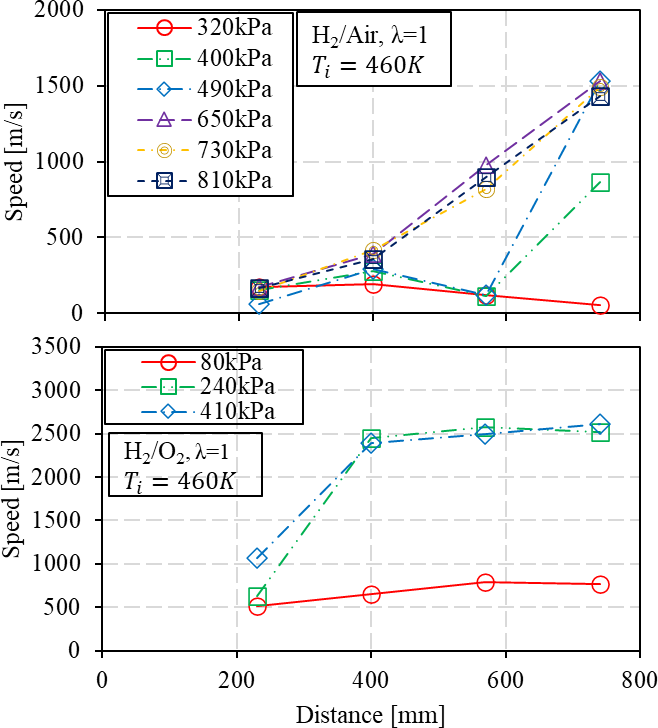
Figure 14. Effect of pressure on DDT process of H2/air and H2/O2 at temperature 460 K.
Under the higher initial temperature, the reduction on combustion duration can be evident with increasing initial pressure with the various dilution ratio of N2 mixtures as shown in Figure 15. When the H2/air mixture is utilized, the combustion duration can be shortened to less than 2 ms with a higher initial pressure of 810 kPa. Unlike the ambient temperature, the improvement is not significant. Furthermore, by utilizing pure oxygen and an initial pressure of 400 kPa, the combustion duration can be lowered to less than 0.5 ms. This is due to the fully developed steady detonation from the transition.
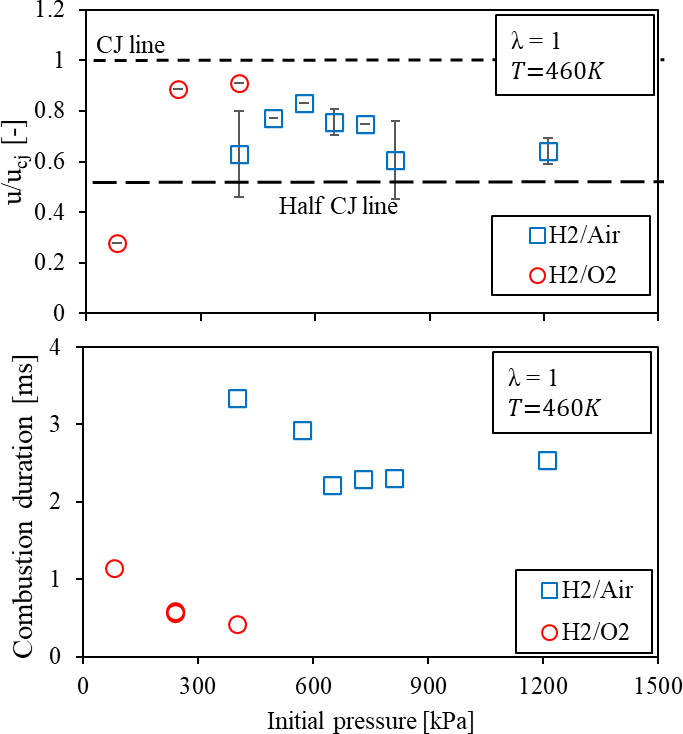
Figure 15. Pressure and oxygen enrichment impact on flame speed and the requisite duration to approach the end of the tube under the temperature of 460 K.
3.5. Effect of Temperature on H2/air Mixture under Pressure 650 kPa
As discussed above, the higher initial temperature promotes the chemical reaction to allow the flame to accelerate above the half C-J velocity with increased initial pressure even though the N2 dilution ratio is increased. In this section, the effect of thermodynamic conditions on the flame propagation speed is further demonstrated within the range of 300 to 460 K using the H2/air mixture under the pressure of 650 kPa, as shown in Figure 16A. The spark timing is adjusted to modulate the background temperature after the end of compression. Flame speed exhibited a gradual increase along the measurement points for all cases. Especially from measurement point 4, the flame acceleration becomes evident with the increased temperature. The results suggest that the temperature is beneficial to increase the flame acceleration when the energy density remains the same. Even though the mixture is diluted with air, given the current tube geometry, the potential for achieving DDT can be promoted with elevated thermodynamic conditions. The flame speed at measurement point 4 is compared with steady CJ velocity to observe the status of flame propagation, as shown in Figure 16B. Flame speed is challenged to achieve half CJ speed when the temperature is at ambient condition. The improvement is becoming apparent as it exceeds half CJ velocity and approaches the CJ velocity with greatly elevated temperature. However, the impact becomes to diminish at temperatures beyond 350 K. This suggests the temperature impact is not sufficient to approach the steady CJ velocity under the fixed energy density and current tube length.
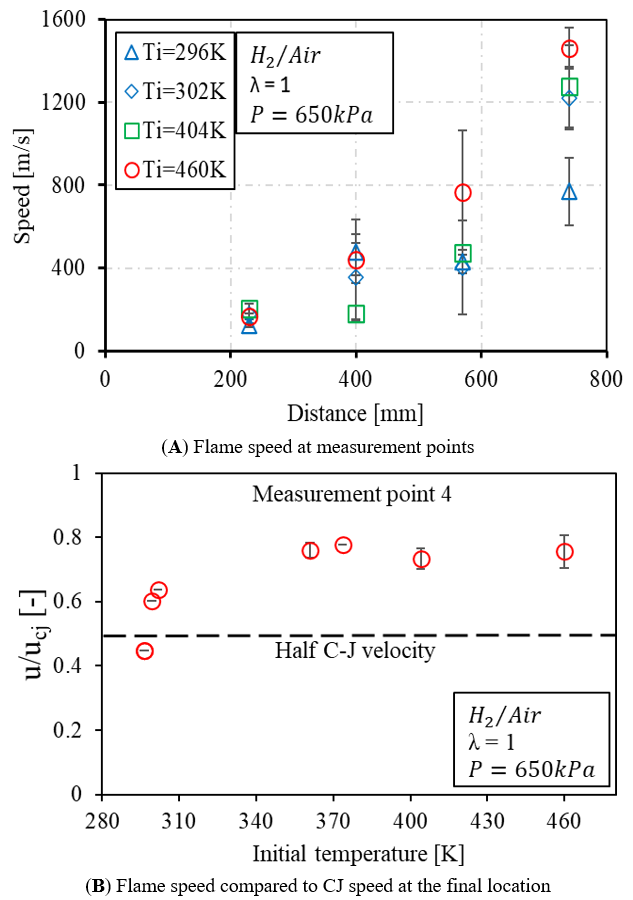
Figure 16. The effect of initial temperature on flame speed using the H2/Air mixture.
4. Conclusions
The research presents a novel approach utilizing a rapid compression machine with a detonation tube to investigate the deflagration to detonation transition process of premixed mixtures at high initial pressure and temperature. A mixture of H2 fuel with various N2 dilution fractions is employed to modify the reactivity of the mixture. This includes the range covered from air to pure oxygen conditions. The purpose is to characterize their DDT process in a detonation tube with an inner diameter of 11.1 mm. The main conclusions are given below:
(1) Flame propagation speed is determined by both ion current and pressure measurement along the length of the tube. The slopes of the ion sensor and pressure sensor align closely at each measurement point upon the detonation wave. However, the ion sensor demonstrates a distinct flame arrival timing as the deflagration wave is approaching, but the pressure waves may lead to incorrect timing if considering the pressure sensor for the flame detection method.
(2) An effective pressure range exists for each mixture, where the elevated initial pressure can change the propensity of the DDT process. Below the initial pressure threshold, the DDT process cannot be initiated; a good correlation is observed between the initial pressure and the flame speed acceleration for all dilution cases. The range is closely related to the reactivity of the mixture. Oxygen enrichment increases energy density and considerably elevates chemical reactivity. Hence, the reduced combustion duration may lead to minimizing heat loss to the wall for approaching the CJ velocity.
(3) The temperature factor enhances the chemical reaction, leading to enhanced flame acceleration. The flame speed of the H2/air mixture increases from approximately 800 m/s to 1500 m/s with elevated thermodynamic conditions under the pressure 650 kPa. An effective temperature is identified, beyond which the impact is insignificant at temperatures exceeding 360 K.
5. Future Work
The flame acceleration for the H2/air case is slow. However, the flame speed increases monotonically, which has the potential to reach detonation velocity eventually, provided the length of the detonation tube is sufficient. However, the relatively short detonation tube is to control the total compression volume to maintain a preferable compression ratio to increase the background pressure and temperature of the mixture via the compression process. The purpose of the present setup is to investigate the impact of initial pressure on the DDT process in a qualitative manner, with detailed recording over the flame speed history. Another detonation tube with an identical inner diameter but much longer length is under preparation to quantitatively characterize the detonation properties of various fuels, including CH4, C3H8, and DME.
Author Contributions: M.Z.: conceptualization, methodology, software; X.Y., L.J.: data curation, writing—original draft preparation; X.Y., L.J.: visualization, investigation; M.Z.: supervision; L.W., N.S.: software, validation; X.Y., L.J.: writing—reviewing and editing. All authors have read and agreed to the published version of the manuscript.
Institutional Review Board Statement: This study does not involve humans or animals.
Data Availability Statement: Not applicable in this study.
Acknowledgments: Special thanks to CCEL colleagues for their efforts and contributions to this research.
Conflicts of Interest: The authors declare that they have no known competing financial interests or personal relationships that could have appeared to influence the work reported in this paper.
References
- Barsun, S.; Cheah, B.; Shelton, J. Renewable 49 Natural Gas in California; California Energy Commission: Sacramento, CA, USA, 2023.
- Karim, G.A. Hydrogen as a spark ignition engine fuel. Int. J. Hydrogen Energy 2003, 28, 569–577.
- Qiang, Y.; Zhao, S.; Su, F.; Wang, F.; Yang, J.; Wang, S.; Ji, C. Experimental and numerical assessment on co-combustion of hydrogen with ammonia in passive pre-chamber engines. Appl. Therm. Eng. 2025, 259, 124919. https://doi.org/10.1016/j.applthermaleng.2024.124919.
- Rueda-Vázquez, J.M.; Serrano, J.; Jiménez-Espadafor, F.J.; Dorado, M.P. Experimental analysis of the effect of hydrogen as the main fuel on the performance and emissions of a modified compression ignition engine with water injection and compression ratio reduction. Appl. Therm. Eng. 2024, 238, 121933. https://doi.org/10.1016/j.applthermaleng.2023.121933.
- Valera-Medina, A.; Xiao, H.; Owen-Jones, M.; David, W.I.F.; Bowen, P.J. Ammonia for power. Prog. Energy Combust. Sci. 2018, 69, 63–102. https://doi.org/10.1016/j.pecs.2018.07.001.
- Nie, X.; Bi, Y.; Shen, L.; Lei, J.; Wan, M.; Wang, Z.; Liu, S.; Huang, F. Combustion and emission characteristics of ammonia-diesel dual fuel engine at different altitudes. Fuel 2024, 371, 132072. https://doi.org/10.1016/j.fuel.2024.132072.
- Reiter, A.J.; Kong, S.-C. Combustion and emissions characteristics of compression-ignition engine using dual ammonia-diesel fuel. Fuel 2011, 90, 87–97. https://doi.org/10.1016/j.fuel.2010.07.055.
- Wei, H.; Zhang, R.; Chen, L.; Pan, J.; Wang, X. Effects of high ignition energy on lean combustion characteristics of natural gas using an optical engine with a high compression ratio. Energy 2021, 223, 120053. https://doi.org/10.1016/j.energy.2021.120053.
- Lee, K.; Bae, C.; Kang, K. The effects of tumble and swirl flows on flame propagation in a four-valve S.I. engine. Appl. Therm. Eng. 2007, 27, 2122–2130. https://doi.org/10.1016/j.applthermaleng.2006.11.011.
- Kaplan, M. Influence of swirl, tumble and squish flows on combustion characteristics and emissions in internal combustion engine-review. Int. J. Automot. Eng. Technol. 2019, 8, 83–102. https://doi.org/10.18245/ijaet.558258.
- Jin, L.; Leblanc, S.; Zhang, X.; Bastable, A.; Tjong, J.; Zheng, M. Impact of Discharge Current Profiling on Ignition Characteristics of Hydrogen/Methane Blends. In Proceedings of the ASME (American Society of Mechanical Engineers) 2022 ICE Forward Conference, Indianapolis, IN, USA, 16–19 October 2022; ISBN 978-0-7918-8654-0: V001T03A001. https://doi.org/10.1115/ICEF2022-88393.
- Yu, X.; Jin, L.; Reader, G.; Wang, M.; Zheng, M. Effective Ignition of Lean Methane/Hydrogen Mixture in a Rapid Compression Machine 2023-01–0255; SAE: Detroit, MI, USA, 2023. https://doi.org/10.4271/2023-01-0255.
- Han, X.; Yu, X.; Zhu, H.; Wang, L.; Yu, S.; Wang, M.; Zheng, M. Elastic breakdown via multi-core high frequency discharge for lean-burn ignition. Proc. Inst. Mech. Eng. Part. D J. Automob. Eng. 2022, 236, 2661–2680. https://doi.org/10.1177/09544070211062278.
- Han, X.; Yu, S.; Tjong, J.; Zheng, M. Study of an innovative three-pole igniter to improve efficiency and stability of gasoline combustion under charge dilution conditions. Appl. Energy 2020, 257, 113999. https://doi.org/10.1016/j.apenergy.2019.113999.
- Corrigan, D.J.; Di Blasio, G.; Ianniello, R.; Silvestri, N.; Breda, S.; Fontanesi, S.; Beatrice, C. Engine Knock Detection Methods for Spark Ignition and Prechamber Combustion Systems in a High-Performance Gasoline Direct Injection Engine. SAE Int. J. Engines 2022, 15, 883–897. https://doi.org/10.4271/03-15-06-0047.
- Yu, X.; Wang, L.; Yu, S.; Wang, M.; Zheng, M. Flame kernel development with radiofrequency oscillating plasma ignition. Plasma Sources Sci. Technol. 2022, 31, 055004. https://doi.org/10.1088/1361-6595/ac5f21.
- Tian, J.; Xiong, Y.; Wang, L.; Wang, Y.; Liu, P.; Shi, X.; Wang, N.; Yin, W.; Cheng, Y.; Zhao, Q. Experimental study of the effect of nanosecond pulse discharge parameters on the methane-air mixture combustion. Fuel 2024, 364, 131166. https://doi.org/10.1016/j.fuel.2024.131166.
- Merotto, L.; Balmelli, M.; Vera-Tudela, W.; Soltic, P. Comparison of ignition and early flame propagation in methane/air mixtures using nanosecond repetitively pulsed discharge and inductive ignition in a pre-chamber setup under engine relevant conditions. Combust. Flame 2022, 237, 111851. https://doi.org/10.1016/j.combustflame.2021.111851.
- Cathey, C.D.; Tang, T.; Shiraishi, T.; Urushihara, T.; Kuthi, A.; Gundersen, M.A. Nanosecond Plasma Ignition for Improved Performance of an Internal Combustion Engine. IEEE Trans. Plasma Sci. 2007, 35, 1664–1668. https://doi.org/10.1109/TPS.2007.907901.
- Alvarez, C.E.C.; Couto, G.E.; Roso, V.R.; Thiriet, A.B.; Valle, R.M. A review of prechamber ignition systems as lean combustion technology for SI engines. Appl. Therm. Eng. 2018, 128, 107–120. https://doi.org/10.1016/j.applthermaleng.2017.08.118.
- Tanoue, K.; Kimura, T.; Jimoto, T.; Hashimoto, J.; Moriyoshi, Y. Study of prechamber combustion characteristics in a rapid compression and expansion machine. Appl. Therm. Eng. 2017, 115, 64–71. https://doi.org/10.1016/j.applthermaleng.2016.12.079.
- Kendall, J. Mahle Liebherr Develop Active Pre Chamber Hydrogen Engine. 2021. Available online: https://www.sae.org/news/2021/11/mahle-liebherr-develop-active-pre-chamber-hydrogen-engine (accessed on 15 April 2025).
- Biswas, S.; Qiao, L. Prechamber Hot Jet Ignition of Ultra-Lean H 2 /Air Mixtures: Effect of Supersonic Jets and Combustion Instability. SAE Int. J. Engines 2016, 9, 1584–1592. https://doi.org/10.4271/2016-01-0795.
- Biswas, S.; Tanvir, S.; Wang, H.; Qiao, L. On ignition mechanisms of premixed CH4/air and H2/air using a hot turbulent jet generated by pre-chamber combustion. Appl. Therm. Eng. 2016, 106, 925–937. https://doi.org/10.1016/j.applthermaleng.2016.06.070.
- Tang, Q.; Sampath, R.; Sharma, P.; Marquez, M.E.; Cenker, E.; Magnotti, G. Study on the effects of narrow-throat pre-chamber geometry on the pre-chamber jet velocity using dual formaldehyde PLIF imaging. Combust. Flame 2022, 240, 111987. https://doi.org/10.1016/j.combustflame.2022.111987.
- Guo, X.; Li, T.; Chen, R.; Huang, S.; Zhou, X.; Wang, N.; Li, S. Effects of the nozzle design parameters on turbulent jet development of active pre-chamber. Energy 2024, 306, 132568. https://doi.org/10.1016/j.energy.2024.132568.
- Braun, E.; Lu, F.; Sagov, M.; Wilson, D.; Grubyi, P. Proof-of-Principle Detonation Driven, Linear Electric Generator Facility. In Proceedings of the 8th Annual International Energy Conversion Engineering Conference, American Institute of Aeronautics and Astronautics, Nashville, TN, USA, 25–28 July 2010; ISBN 978-1-62410-156-4. https://doi.org/10.2514/6.2010-6767.
- Lee, J.H.S. The Detonation Phenomenon; Cambridge University Press: Cambridge, UK, 2008.
- Bussing, T.; Pappas, G. An introduction to pulse detonation engines. In Proceedings of the 32nd Aerospace Sciences Meeting and Exhibit, American Institute of Aeronautics and Astronautics, Reno, NV, USA, 10–13 January 1994. https://doi.org/10.2514/6.1994-263.
- Kailasanath, K. Applications of detonations to propulsion—A review. In Proceedings of the 37th Aerospace Sciences Meeting and Exhibit, American Institute of Aeronautics and Astronautics, Reno, NV, USA, 11–14 January1999. https://doi.org/10.2514/6.1999-1067.
- Razus, D.; Brinzea, V.; Mitu, M.; Oancea, D. Burning Velocity of Liquefied Petroleum Gas (LPG)−Air Mixtures in the Presence of Exhaust Gas. Energy Fuels 2010, 24, 1487–1494. https://doi.org/10.1021/ef901209q.
- Schefer, R.W.; White, C.; Keller, J.; Ca, L. Chapter 8—Lean Hydrogen Combustion. In Lean Combustion; Academic Press: Cambridge, MA, USA, 2008.
- Jacobs, S.; Döntgen, M.; Alquaity, A.B.S.; Kopp, W.A.; Kröger, L.C.; Burke, U.; Pitsch, H.; Leonhard, K.; Curran, H.J.; Heufer, K.A. Detailed kinetic modeling of dimethoxymethane. Part II: Experimental and theoretical study of the kinetics and reaction mechanism. Combust. Flame 2019, 205, 522–533. https://doi.org/10.1016/j.combustflame.2018.12.026.
- Goswami, M.; Bastiaans, R.J.M.; De Goey, L.P.H.; Konnov, A.A. Experimental and modelling study of the effect of elevated pressure on ethane and propane flames. Fuel 2016, 166, 410–418. https://doi.org/10.1016/j.fuel.2015.11.013.
- Luo, C.; Yu, Z.; Wang, Y.; Ai, Y. Experimental Investigation of Lean Methane–Air Laminar Premixed Flames at Engine-Relevant Temperatures. ACS Omega 2021, 6, 17977–17987. https://doi.org/10.1021/acsomega.1c01692.
- Sileghem, L.; Alekseev, V.A.; Vancoillie, J.; Nilsson, E.J.K.; Verhelst, S.; Konnov, A.A. Laminar burning velocities of primary reference fuels and simple alcohols. Fuel 2014, 115, 32–40. https://doi.org/10.1016/j.fuel.2013.07.004.
- Huzayyin, A.S.; Moneib, H.A.; Shehatta, M.S.; Attia, A.M.A. Laminar burning velocity and explosion index of LPG–air and propane–air mixtures. Fuel 2008, 87, 39–57. https://doi.org/10.1016/j.fuel.2007.04.001.
- Dirrenberger, P.; Glaude, P.A.; Bounaceur, R.; Le Gall, H.; Da Cruz, A.P.; Konnov, A.A.; Battin-Leclerc, F. Laminar burning velocity of gasolines with addition of ethanol. Fuel 2014, 115, 162–169. https://doi.org/10.1016/j.fuel.2013.07.015.
- De Vries, J.; Lowry, W.B.; Serinyel, Z.; Curran, H.J.; Petersen, E.L. Laminar flame speed measurements of dimethyl ether in air at pressures up to 10 atm. Fuel 2011, 90, 331–338. https://doi.org/10.1016/j.fuel.2010.07.040.
- Adusumilli, S.; Seitzman, J. Laminar flame speed measurements of ethylene at high preheat temperatures and for diluted oxidizers. Combust. Flame 2021, 233, 111564. https://doi.org/10.1016/j.combustflame.2021.111564.
- Rokni, E.; Moghaddas, A.; Askari, O.; Metghalchi, H. Measurement of Laminar Burning Speeds and Investigation of Flame Stability of Acetylene (C2H2)/Air Mixtures. J. Energy Resour. Technol. 2015, 137, 012204. https://doi.org/10.1115/1.4028363.
- Gillespie, F.; Metcalfe, W.K.; Dirrenberger, P.; Herbinet, O.; Glaude, P.-A.; Battin-Leclerc, F.; Curran, H.J. Measurements of flat-flame velocities of diethyl ether in air. Energy 2012, 43, 140–145. https://doi.org/10.1016/j.energy.2012.01.021.
- Dirrenberger, P.; Le Gall, H.; Bounaceur, R.; Glaude, P.-A.; Battin-Leclerc, F. Measurements of Laminar Burning Velocities above Atmospheric Pressure Using the Heat Flux Method—Application to the Case of n-Pentane. Energy Fuels 2015, 29, 398–404. https://doi.org/10.1021/ef502036j.
- Kindracki, J. Study of detonation initiation in kerosene–oxidizer mixtures in short tubes. Shock Waves 2014, 24, 603–618. https://doi.org/10.1007/s00193-014-0519-2.
- Guirao, C.M.; Knystautas, R.; Lee, J.H. A Summary of Hydrogen Air Detonation Experiments; U.S. Nuclear Regulatory Commission: Washington, DC, USA, 1989.
- Kuznetsov, M.; Alekseev, V.; Matsukov, I.; Dorofeev, S. DDT in a smooth tube filled with a hydrogen–oxygen mixture. Shock Waves 2005, 14, 205–215. https://doi.org/10.1007/s00193-005-0265-6.
- United States Nuclear Regulatiory Commission. Three Mile Island Accident. Available online: https://www.nrc.gov/docs/ML0825/ML082560250.pdf (accessed on 15 April 2025).
- Manzhalei, V.I.; Mitrofanov, V.V.; Subbotin, V.A. Measurement of inhomogeneities of a detonation front in gas mixtures at elevated pressures. Combust. Explos. Shock Waves 1974, 10, 89–95. https://doi.org/10.1007/BF01463793.
- Shen, X.; Fu, W.; Liang, W.; Wen, J.X.; Liu, H.; Law, C.K. Strong flame acceleration and detonation limit of hydrogen-oxygen mixture at cryogenic temperature. Proc. Combust. Inst. 2023, 39, 2967–2977. https://doi.org/10.1016/j.proci.2022.07.005.
- Ciccarelli, G.; Boccio, J.L.; Ginsberg, T.; Finfrock, C.; Gerlach, L.; Tagawa, H.; Malliakos, A. Hydrogen Detonation and Detonation Transition Data from The High-Temperature Combustion Facility; Brookhaven National Lab. (BNL): Upton, NY, USA, 1995.
- Bangalore Venkatesh, P.; Graziano, T.; Bane, S.P.; Meyer, S.; Grubelich, M.C. Deflagration-to-Detonation Transition in Nitrous Oxide-Ethylene Mixtures and its Application to Pulsed Propulsion Systems. In Proceedings of the 55th AIAA Aerospace Sciences Meeting, American Institute of Aeronautics and Astronautics, Grapevine, TX, USA, 9–13 January 2017; ISBN 978-1-62410-447-3. https://doi.org/10.2514/6.2017-0372.
- Tieszen, S.R.; Sherman, M.P.; Benedick, W.B.; Berman, M. Detonability of H2 Air Diluent Mixtures; U.S. Nuclear Regulatory Commission: Washington, DC, USA, 1987.
- Wu, M.; Burke, M.P.; Son, S.F.; Yetter, R.A. Flame acceleration and the transition to detonation of stoichiometric ethylene/oxygen in microscale tubes. Proc. Combust. Inst. 2007, 31, 2429–2436. https://doi.org/10.1016/j.proci.2006.08.098.
- Li, J.; Pan, J.; Jiang, C.; Ni, J.; Pan, Z.; Otchere, P. Effect of hydrogen addition on the detonation performances of methane/oxygen at different equivalence ratios. Int. J. Hydrogen Energy 2019, 44, 27974–27983. https://doi.org/10.1016/j.ijhydene.2019.09.016.
- Kuznetsov, M.; Ciccarelli, G.; Dorofeev, S.; Alekseev, V.; Yankin Yu Kim, T.H. DDT in methane-air mixtures. Shock Waves 2002, 12, 215–220. https://doi.org/10.1007/s00193-002-0155-0.
- Saif, M.; Wang, W.; Pekalski, A.; Levin, M.; Radulescu, M.I. Chapman Jouguet deflagrations and their transition to detonation. Proc. Combust. Inst. 2017, 36, 2771–2779. https://doi.org/10.1016/j.proci.2016.07.122.
- Litchfield, E.L.; Hay, M.H.; Forshey, D.R. Direct electrical initiation of freely expanding gaseous detonation waves. In Symposium (International) on Combustion; Elsevier: Amsterdam, The Netherlands, 1963.
- Zitoun, R.; Desbordes, D.; Guerraud, C.; Deshaies, B. Direct initiation of detonation in cryogenic gaseous H2-O2 mixtures. Shock Waves 1995, 4, 331–337
- Matsui, H.; Lee, J.H. On the measure of the relative detonation hazards of gaseous fuel-oxygen and air mixtures. Symp. Combust. 1979, 17, 1269–1280. https://doi.org/10.1016/S0082-0784(79)80120-4.
- Desbordes, D. Aspects Stationnaires et Transitoires de la Détonation dans les gaz: Relation Avec la Structure Cellulaire du Front. Ph.D. Thesis, University of Poitiers, Poitiers, France, 1990.
- Knystautas, R.; Lee, J.H.; Guirao, C.M. The critical tube diameter for detonation failure in hydrocarbon-air mixtures. Combust. Flame 1982, 48, 63–83. https://doi.org/10.1016/0010-2180(82)90116-X.
- Strehlow, R.A.; Maurer, R.E.; Rajan, S. Transverse waves in detonations. I—Spacing in the hydrogen-oxygen system. AIAA J. 1969, 7, 323–328. https://doi.org/10.2514/3.5093.
- Strehlow, R.A.; Engel, C.D. Transverse waves in detonations. II—Structure and spacing in H2–O2, C2H2–O2, and CH4–O2 systems. AIAA J. 1969, 7, 492–496. https://doi.org/10.2514/3.5134.
- Liberman, M.A.; Ivanov, M.F.; Kiverin, A.D.; Kuznetsov, M.S.; Chukalovsky, A.A.; Rakhimova, T.V. Deflagration-to-detonation transition in highly reactive combustible mixtures. Acta Astronaut. 2010, 67, 688–701. https://doi.org/10.1016/j.actaastro.2010.05.024.
- Lee, J.H.; Matsui, H. A comparison of the critical energies for direct initiation of spherical detonations in acetylene oxygen mixtures. Combust. Flame 1977, 28, 61–66. https://doi.org/10.1016/0010-2180(77)90008-6.
- Voytsekhovskiy, B.V.; Mitrofanov, V.V.; Topchiyan, M.E. The structure of a detonation front in gases. Combust. Explos. Shock. Waves 1969, 5, 267–273.
- Wang, C.; Wu, S.; Zhao, Y.; Addai, E.K. Experimental investigation on explosion flame propagation of H2-O2 in a small scale pipeline. J. Loss Prev. Process Ind. 2017, 49, 612–619. https://doi.org/10.1016/j.jlp.2017.06.004.
- Bykov, V.; Koksharov, A.; Kuznetsov, M.; Zhukov, V.P. Hydrogen-oxygen flame acceleration in narrow open ended channels. Combust. Flame 2022, 238, 111913. https://doi.org/10.1016/j.combustflame.2021.111913.
- Denisov, Y.N.; Troshin, Y.K. The fine structure of spinning detonation. Combust. Flame 1971, 16, 141–145. https://doi.org/10.1016/S0010-2180(71)80079-2.
- Barthel, H.O. Predicted spacings in hydrogen-oxygen-argon detonations. Phys. Fluids 1974, 17, 1547–1553. https://doi.org/10.1063/1.1694932.
- Agafonov, G.L.; Frolov, S.M. Computation of the detonation limits in gaseous hydrogen-containing mixtures. Combust. Explos. Shock Waves 1994, 30, 91–100. https://doi.org/10.1007/BF00787891.
- Benedick, W.B.; Knystautas, R.; Lee, J.H.S. (Eds.) Large Scale Experiments on the Transmission of Fuel Air Detonations from Two Dimensional Channels; AIAA: Reston, VA, USA, 1983. https://doi.org/10.2514/4.865695.
- Ciccarelli, G.; Ginsberg, T.; Boccio, J.L. Detonation Cell Size Measurements in High-Temperature Hydrogen-Air-Steam Mixtures at the BNL High-Temperature Combustion Facility. 1997. Available online: https://www.osti.gov/servlets/purl/563843-ETGbv5/webviewable/ (accessed on 15 April 2025).
- Stamps, D.; Benedick, W.; Tieszen, S. Hydrogen Air Diluent Detonation Study for Nuclear Reactor Safety Analyses. 1991. Available online: https://www.osti.gov/servlets/purl/6119703/ (accessed on 15 April 2025).
- Stamps, D.W.; Tieszen, S.R. The influence of initial pressure and temperature on hydrogen-air-diluent detonations. Combust. Flame 1991, 83, 353–364. https://doi.org/10.1016/0010-2180(91)90082-M.
- Kaneshige, M.J. Gaseous Detonation Initiation and Stabilization by Hypervelocity Projectiles; California Institute of Technology: Pasadena, CA, USA, 1999.
- Guirao, C.M.; Knystautas, R.; Lee, J.H.; Benedick, W.; Berman, M. Hydrogen air detonations. Symp. Combust. 1982, 19, 583–590. https://doi.org/10.1016/S0082-0784(82)80232-4.
- Wang, B.L.; Olivier, H.; Grönig, H. Ignition of shock-heated H2-air-steam mixtures. Combust. Flame 2003, 133, 93–106. https://doi.org/10.1016/S0010-2180(02)00552-7.
- Cross, M.; Ciccarelli, G. DDT and detonation propagation limits in an obstacle filled tube. J. Loss Prev. Process Ind. 2015, 36, 380–386. https://doi.org/10.1016/j.jlp.2014.11.020.
- Bull, D.C.; Elsworth, J.E.; Shuff, P.J.; Metcalfe, E. Detonation cell structures in fuel/air mixtures. Combust. Flame 1982, 45, 7–22. https://doi.org/10.1016/0010-2180(82)90028-1.
- Atkinson, R.; Bull, D.C.; Shuff, P.J. Initiation of spherical detonation in hydrogenair. Combust. Flame 1980, 39, 287–300. https://doi.org/10.1016/0010-2180(80)90025-5.
- Dorofeev, S.B.; Sidorov, V.P.; Kuznetsov, M.S.; Matsukov, I.D.; Alekseev, V.I. Effect of scale on the onset of detonations. Shock Waves 2000, 10, 137–149. https://doi.org/10.1007/s001930050187.
- Makeev, V.I.; Gostintsev, Y.A.; Strogonov, V.V.; Bokhon, Y.A.; Chernushkin, Y.N.; Kulikov, V.N. Combustion and detonation of hydrogen air mixtures in free spaces. Combust. Explos. Shock Waves 1983, 19, 548–550. https://doi.org/10.1007/BF00750415.
- Kumar, R.K. Detonation cell widths in hydrogen oxygen diluent mixtures. Combust. Flame 1990, 80, 157–169. https://doi.org/10.1016/0010-2180(90)90124-A.
- Anderson, T.J.; Dabora, E.K. Measurements of normal detonation wave structure using Rayleigh imaging. Symp. Combust. 1992, 24, 1853–1860. https://doi.org/10.1016/S0082-0784(06)80217-1.
- Liu, Y.K.; Lee, J.H.; Knystautas, R. Effect of Geometry on the Transmimion of Detonation through an Orifice. Combust. Flame 1984, 56, 215–225.
- Jin, L. Experimental Improvements of a Rapid Compression Machine. Master’s Thesis, University of Windsor, Windsor, ON, Canada, 2022.
- Jin, L.; Yu, X.; Wang, M.; Reader, G.; Zheng, M. Effect of spark assisted compression ignition on the end-gas autoignition with DME-air mixtures in a rapid compression machine. SAE: Detroit, MI, USA, 2024. https://doi.org/10.4271/2024-01-2822.
- Gavrikov, A.I.; Efimenko, A.A.; Dorofeev, S.B. A model for detonation cell size prediction from chemical kinetics. Combust. Flame 2000, 120, 19–33. https://doi.org/10.1016/S0010-2180(99)00076-0.
- Ng, H.; Ju, Y.; Lee, J. Assessment of detonation hazards in high-pressure hydrogen storage from chemical sensitivity analysis. Int. J. Hydrogen Energy 2007, 32, 93–99. https://doi.org/10.1016/j.ijhydene.2006.03.012.
- Shchelkin, K.I.; Troshin, Y.K. Gasdynamics of Combustion; Mono Book Corp.: Baltimore, MD, USA, 1965.